Simple programming of complex machining procedures
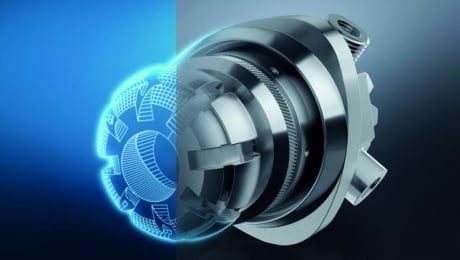
Exclusive DMG MORI technology cycles increase process reliability and quality in workshop-oriented programming
In order to optimally use the whole potential of today’s machine tools, a large portion of expert competence is needed. Increasingly complex applications require ever more sophisticated machining strategies, that can only be realised with high programming effort under conventional conditions. DMG MORI as competence partner supports its customers also at the preliminary stage of metal cutting manufacturing with a large number of exclusive DMG MORI technology cycles, which contribute to process reliability mainly in workshop-oriented programming, improve component qualities and also enable integration of technology.
Despite increasing automation within the metal-cutting process chain, workshop-oriented programming is still of great importance especially in single item production and the production of small and medium-sized quantities. On the one hand, skilled workers can optimally use their process competence with this, on the other, short-term modifications can be responded to directly. A crucial role for the productivity of workshop-oriented programming are special machining cycles with which recurring machining operations can be automatically created as far as possible or integrated into the program sequence. The operator only needs to enter elementary parameters via a context menu. All required calculations as well as the creation of the respective sentences occur afterwards at the press of a button.
Working with cycles is now state of the art, whereby standard cycles for turning, milling and drilling are included in the performance range of modern controls. DMG MORI has been developing its own technology cycles for its customers beyond this standard for many years, based on its varied application experience. These are used to program even complex machining steps by simply entering the parameters directly on the machine in the dialog. 5-axis simultaneous machining, gear cutting and turn & mill complete machining are just three examples of the complex applications with which DMG MORI is dealing time and again in this field.
With the exclusive technology cycles, DMG MORI sustainably supports the work of its customers on the powerful machine tools at multiple levels. Advantages, in addition to the higher ease of use and reduced cycle times, also include process reliability as well as component quality. Adding to this is the option of technology integration. So there are special technology cycles for interior, exterior and surface grinding, as well as cycles for calibrating the dressing station and dressing the grinding wheel. A special measuring technology of solid-bourne sound was developed for scratching the grinding wheel on the component. Dressing of the grinding wheel can also be automated with this solution, thus ensuring a reliable process. Grinding operations can thus be performed during low-manned machine operation. The component quality is ensured with In Process measurement by means of a measuring probe.
Another example of this is the new DMG MORI gearSKIVING. This technology cycle enables a dialog-based production of toothed wheels by means of the innovative hob peeling procedure, which is to be regarded at the same level as established but conservative procedures like gear shaping and hobbing. This enables eight times faster machining and gear qualities of DIN 7 of both straight-cut as well as helical-cut outer and inner spur gears and spline shaft gearing compared to gear shaping. Even toothed wheels on shoulders can be produced without damage with this. The production chain can be significantly reduced with DMG MORI gearSKIVING. During turning as well as milling, complete machining occurs on a single DMG MORI machine tool. Special machines are not needed for many applications. The setup operations no longer needed in combination with the relatively high chip volume due to DMG MORI gearSKIVING reduce idle times and guarantee high productivity. A competent DMG MORI teams also provides turnkey solutions including tool design, enabling DMG MORI to meet customer requirements explicitly already during purchase advice, and to create an optimum complete package.
Equally complex is the free-form milling in 5-axis simultaneous machining. The respective DMG MORI technology cycle is able to machine free-form surfaces with 5-axis interpolation at the main and counter spindle as well as turning and milling with interpolating B-axis. Tool and mould manufacturing, the aerospace industry and medical engineering are just three exemplary industries that can significantly reduce the programming effort with this.
Productivity, process integration and reliability with DMG MORI technology cycles
Due to the growing shortage of skilled personnel, the challenge to produce complex workpieces economically and with the required quality is on the increase. This is also why companies benefit from the support of DMG MORI technology cycles. Less previous knowledge is needed for simple program creation, while the time saved in programming ensures higher machine availability. And the same applies to more efficient and in may cases faster machining.
The benefits of the DMG MORI technology cycles also extend to the component and surface quality as well as the shape accuracy and process reliability. The automated procedures protect the machine, component and tools equally, enabling production without risks.
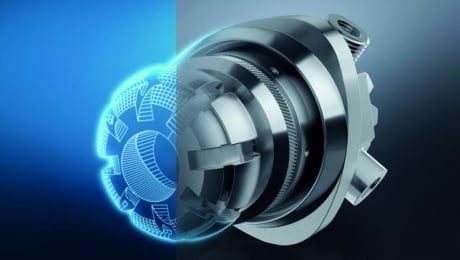
Exclusive DMG MORI technology cycles increase process reliability and quality in workshop-oriented programming
In order to optimally use the whole potential of today’s machine tools, a large portion of expert competence is needed. Increasingly complex applications require ever more sophisticated machining strategies, that can only be realised with high programming effort under conventional conditions. DMG MORI as competence partner supports its customers also at the preliminary stage of metal cutting manufacturing with a large number of exclusive DMG MORI technology cycles, which contribute to process reliability mainly in workshop-oriented programming, improve component qualities and also enable integration of technology.
Despite increasing automation within the metal-cutting process chain, workshop-oriented programming is still of great importance especially in single item production and the production of small and medium-sized quantities. On the one hand, skilled workers can optimally use their process competence with this, on the other, short-term modifications can be responded to directly. A crucial role for the productivity of workshop-oriented programming are special machining cycles with which recurring machining operations can be automatically created as far as possible or integrated into the program sequence. The operator only needs to enter elementary parameters via a context menu. All required calculations as well as the creation of the respective sentences occur afterwards at the press of a button.
Working with cycles is now state of the art, whereby standard cycles for turning, milling and drilling are included in the performance range of modern controls. DMG MORI has been developing its own technology cycles for its customers beyond this standard for many years, based on its varied application experience. These are used to program even complex machining steps by simply entering the parameters directly on the machine in the dialog. 5-axis simultaneous machining, gear cutting and turn & mill complete machining are just three examples of the complex applications with which DMG MORI is dealing time and again in this field.
With the exclusive technology cycles, DMG MORI sustainably supports the work of its customers on the powerful machine tools at multiple levels. Advantages, in addition to the higher ease of use and reduced cycle times, also include process reliability as well as component quality. Adding to this is the option of technology integration. So there are special technology cycles for interior, exterior and surface grinding, as well as cycles for calibrating the dressing station and dressing the grinding wheel. A special measuring technology of solid-bourne sound was developed for scratching the grinding wheel on the component. Dressing of the grinding wheel can also be automated with this solution, thus ensuring a reliable process. Grinding operations can thus be performed during low-manned machine operation. The component quality is ensured with In Process measurement by means of a measuring probe.
Another example of this is the new DMG MORI gearSKIVING. This technology cycle enables a dialog-based production of toothed wheels by means of the innovative hob peeling procedure, which is to be regarded at the same level as established but conservative procedures like gear shaping and hobbing. This enables eight times faster machining and gear qualities of DIN 7 of both straight-cut as well as helical-cut outer and inner spur gears and spline shaft gearing compared to gear shaping. Even toothed wheels on shoulders can be produced without damage with this. The production chain can be significantly reduced with DMG MORI gearSKIVING. During turning as well as milling, complete machining occurs on a single DMG MORI machine tool. Special machines are not needed for many applications. The setup operations no longer needed in combination with the relatively high chip volume due to DMG MORI gearSKIVING reduce idle times and guarantee high productivity. A competent DMG MORI teams also provides turnkey solutions including tool design, enabling DMG MORI to meet customer requirements explicitly already during purchase advice, and to create an optimum complete package.
Equally complex is the free-form milling in 5-axis simultaneous machining. The respective DMG MORI technology cycle is able to machine free-form surfaces with 5-axis interpolation at the main and counter spindle as well as turning and milling with interpolating B-axis. Tool and mould manufacturing, the aerospace industry and medical engineering are just three exemplary industries that can significantly reduce the programming effort with this.
Productivity, process integration and reliability with DMG MORI technology cycles
Due to the growing shortage of skilled personnel, the challenge to produce complex workpieces economically and with the required quality is on the increase. This is also why companies benefit from the support of DMG MORI technology cycles. Less previous knowledge is needed for simple program creation, while the time saved in programming ensures higher machine availability. And the same applies to more efficient and in may cases faster machining.
The benefits of the DMG MORI technology cycles also extend to the component and surface quality as well as the shape accuracy and process reliability. The automated procedures protect the machine, component and tools equally, enabling production without risks.