
Production
New Breed of Facemills Offers Versatility
Lightweighting has become more popular in automotive and aerospace for increasing fuel efficiencies. As a result, manufacturers need faster, more efficient facemilling techniques to handle difficult-to-machine materials, such as high-silicon aluminum and other abrasive materials. Speeding up machining processes is always critical. Many of the newer facemills can perform both roughing and finishing operations, extend tool life and boost productivity to help shops lower costs.
Some of the newest facemills are PCD or polycrystalline cubic boron nitride (PCBN) tools, which are typically used for machining the most abrasive materials, particularly in automotive engine applications for machining critical surfaces that require real flatness. These facemills also target bimetal machining, such as gray cast-iron cylinder sleeves in aluminum engine blocks.
Facemills that can rough and finish are highly advantageous in a shop. “Not very often do you see customers wanting to have roughing facemills and then a finishing facemill,” said Tim Aydt, product manager of indexable milling at Troy, Michigan-based Seco Tools LLC. “It’s all dependent on the finish requirements and on machine capabilities. We try to look at everything and establish the best possible outcome for the customer.”

Sandvik Coromant’s new M610 bimetal cutter targets automotive engine applications for finishing aluminum blocks with gray cast-iron sleeves. Image courtesy of Sandvik Coromant
If a customer’s machining carousel is crowded, then “chances are that facemilling is going to be a combined operation,” he added. “It’s going to take the material off the top to rough it and clean it off, and it’s probably going to act as a finishing cutter as well.”
Many traditional facemills feature lead angles that range from 45° to 68° and are often for roughing and finishing, Aydt said, noting that facemilling is generally the first operation performed on a part. Seco recently announced its Double Quattromill 22 facemill, which allows users to take a large DOC while offering freer cutting than the company’s earlier Double Octomill facemills.
“This version of facemill is something we haven’t had, in that it offers a very large depth-of-cut capability,” Aydt said. “To take advantage of that capability, you need a fairly large machine with significant torque and horsepower in order to use that tool to its full advantage. The Double Octomill, with 16 cutting edges, is more economical. While the Double Quattromill 22 offers eight cutting edges, it’s much freer cutting. That’s an advantage with certain high-tech materials.”
The new cutters come in three insert ranges with different edges and grade options. The most common, the ME12 geometry, is effective for cutting stainless steel and superalloys, with edge protection and positive rake, Aydt said. The M12 geometry comes in many grades for compatibility with most workpiece materials, and the M18 cuts steel and cast iron that require heavier edge protection.
Combo Cutters
With automotive applications that require machining aluminum blocks and cylinders with cast-iron sleeves, facemills typically are the first step in the machining process, said Joe DeRoss, milling specialist for Sandvik Coromant Co., Fair Lawn, New Jersey.
“The part is either cast or it comes in as a raw material (bar stock), so you have to machine it to near net shape or net shape to get started,” DeRoss said. “Facemills today are so versatile you can also finish by changing inserts.” He added that switching to the finishing insert is easy with a Coro-mill close-pitch cutter, which has up to 12 cutting edges per insert.
“You can get what we call close pitch, which lets you remove a lot of material faster with better finishes,” he said. Choosing a cutter pitch depends on the workpiece material, the required surface quality, the machine’s horsepower and the stability of a setup.
The more inserts applied, the more draw on horsepower, he added, which is a big factor to consider. The close-pitch cutters result in short chips.
“Aerospace and automotive are the highest users,” DeRoss said. “Especially in automotive, there’s a lot of cast-iron materials, so you can get away with close-pitch cutters.”
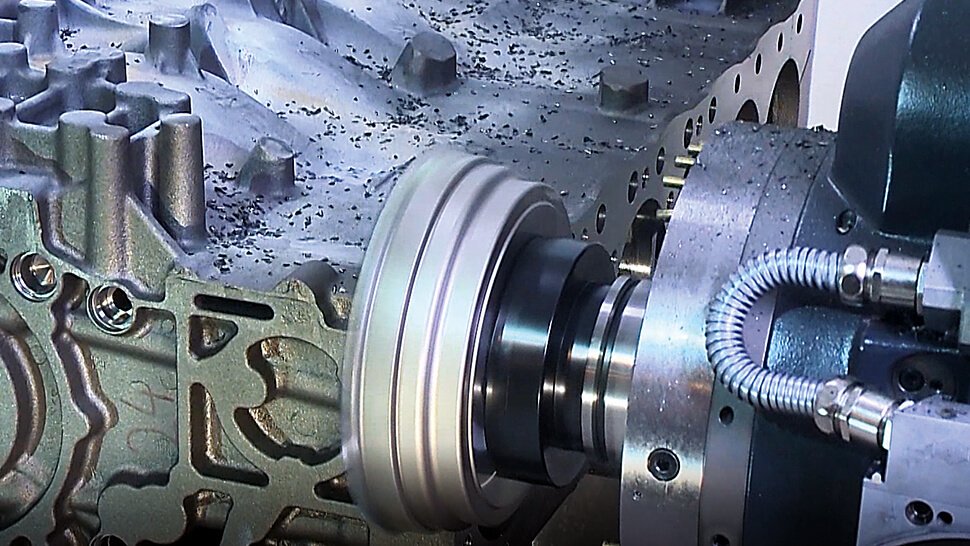
Ingersoll’s new insert series in the octagon facemill family, shown in an automotive finishing operation, includes several carbide, a silicon nitride and two PCBN grades. Image courtesy of Ingersoll Cutting Tool
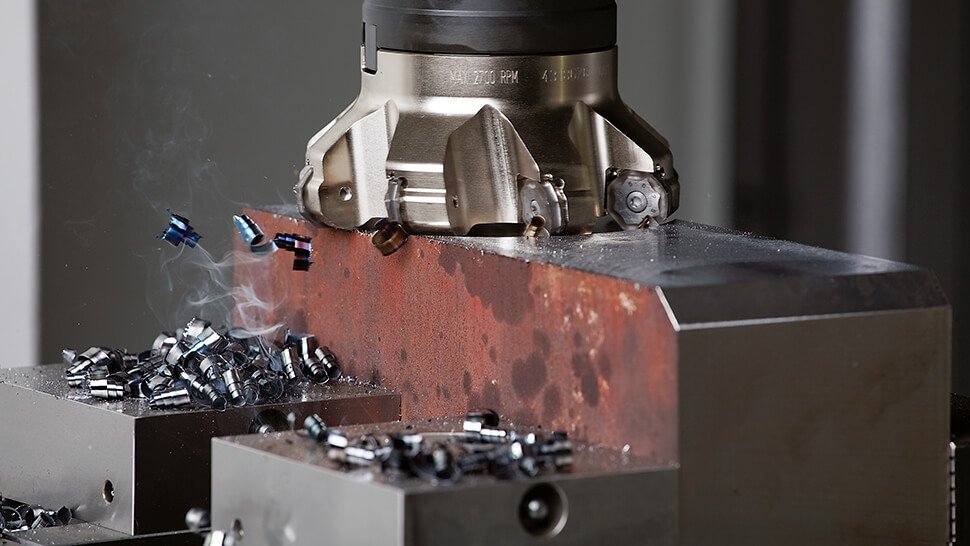
Image courtesy of Seco Tools
Sandvik Coromant’s facemill lineup includes dozens of cutters with varying geometries, pitches and lead angles, he said, including coarse pitch, medium pitch and central lead angles.
Among the latest offerings is the M610 bimetal cutter targeted at automotive engine applications for machining gray cast-iron blocks with aluminum cylinder sleeves. Another, the M5B90, is aimed at all-aluminum applications.
“If it’s really abrasive material, you want something like PCBN,” DeRoss said. He explained that cast iron is very abrasive; its structure doesn’t allow it to chip well. “For high-silicon abrasive materials, like aluminums, you’d probably want to use PCD.”
Automotive engine blocks have two different types of material: cast iron and aluminum. DeRoss said the M610 cutter’s PCBN insert can cut both materials without leaving burrs and scratches on the surface. “It’s a real clean cut, and it’s a finishing operation, giving you a nice finish. It doesn’t flake the edges off of cast iron. Sometimes cast iron gives you what’s called frittering. The M610 eliminates frittering and also cuts the aluminum cleanly.”
In the past, DeRoss noted, the whole block would have been cast iron. Manufacturers didn’t worry about weight, even though it meant more fuel consumption. “Now everyone’s trying to go lighter, but all-aluminum blocks are not a great solution for longevity. So they are using aluminum with cast-iron sleeves.”
Whereas most cutters on the market have adjustments for inserts that need to be pre-adjusted up and down, the M610 cutter requires no adjustments. “This is just load it up and run it,” DeRoss said.
As previously noted, the M5B90 is for facemilling aluminum, such as finishing aluminum automotive heads. “It’s definitely made for aluminum parts to remove burrs,” DeRoss said. “Aluminum is soft, but with the silicon content, you need tools that not only last a long time cutting aluminum but also control chips and burring.”
Superhard Cutters
Ingersoll Cutting Tool Co., Rockford, Illinois, offers PCBN and PCD facemills. Ingersoll is the representative in North America of Italian toolmaker IT.TE.DI. SRL, which makes standard and special PCD and PCBN tools, noted Don Yordy, Ingersoll’s team leader for standard milling product development and marketing.
“Demand for facing abrasive aluminum and gray-iron components, typically powertrain components, has historically driven our development of PCD and PCBN facemills,” Yordy said. “Industries include automotive, light and heavy truck, agriculture, mining, oil and gas, marine and rail.”
The industries that produce engines and transmissions for on-road vehicles tend to drive most of Ingersoll’s milling developments—PCD to rough and finish aluminum-silicon alloys and PCBN to finish gray-iron components.

One of the new Sandvik Coromant facemilling tools, the M5F90, is shown facemilling an aluminum automotive part. This cutter enables roughing and finishing aluminum parts in a single operation, and machining parts without burring, scratching or chipping. Image courtesy of Sandvik Coromant
Requirements to improve power, fuel and emission efficiencies filter down to the feature level, especially for engine combustion faces, Yordy said. “Surface quality specifications have resulted in increased demand for generating and sustaining lower cutting forces when finishing facemills.”
He explained that by forming thinner chips at higher surface velocities, PCD and PCBN can help efficiently mill with reduced cutting forces, increased edge life and equivalent or decreased cycle times when compared with facemills that accept indexable carbide inserts.
Ingersoll recently developed an insert series that includes several carbide, a silicon-nitride and two PCBN grades. According to Yordy, the PCBN inserts ave either a durable negative rake with a landed edge that can be broadly applied or a keen positive, laser-ablated rake face with a sharp edge for the freest possible chip formation. All the inserts—carbide, SiN and PCBN—sit in the pocket with negative axial inclination and provide a larger seating area than other designs that have the same inscribed circle size but with a positive axial inclination. For wear detection and to identify unused edges, both styles of PCBN inserts are thinly coated with gold-colored TiN.
Another finishing facemill from Ingersoll is an axially and radially stepped finishing facemill that can accept carbide, SiN, PCBN or PCD inserts. The radial and axial stepping allows efficient chip formation, which produces low cutting forces and low face pressure while enabling relatively high feed rates, Yordy said. The axial stepping ensures that the crowned wiper is left to remove only 0.002" to 0.003" of material when imparting the surface finish. Because only one wiper is intended to generate the surface finish, there is no insert adjustment. The ideal application to consider using a stepped finisher is one where the process is limited by face pressure, chatter and/or surface tearing.
Outside of aluminum silicon, both Ingersoll and IT.TE.DI. produce PCD facemills for milling materials like copper alloys, graphite and sintered tungsten, Yordy said. Ingersoll recently began a collaborative project on the state of PCD inserts for milling Ti6Al4V. The company is also evaluating PCBN tools as a possible replacement for grinding hardened steel.
Contact | Author
Patrick Waurzyniak
Freelance Writer
Phone: +1 313-268-3162
Send e-mail
Contact | Contributors
Ingersoll Cutting Tool Co.
Phone: +1 815-387-6600
www.ingersoll-imc.com
Sandvik Coromant Co.
Phone: +1 800-SANDVIK
www.sandvik.coromant.com
Seco Tools LLC
Phone: +1 248-528-5200
www.secotools.com