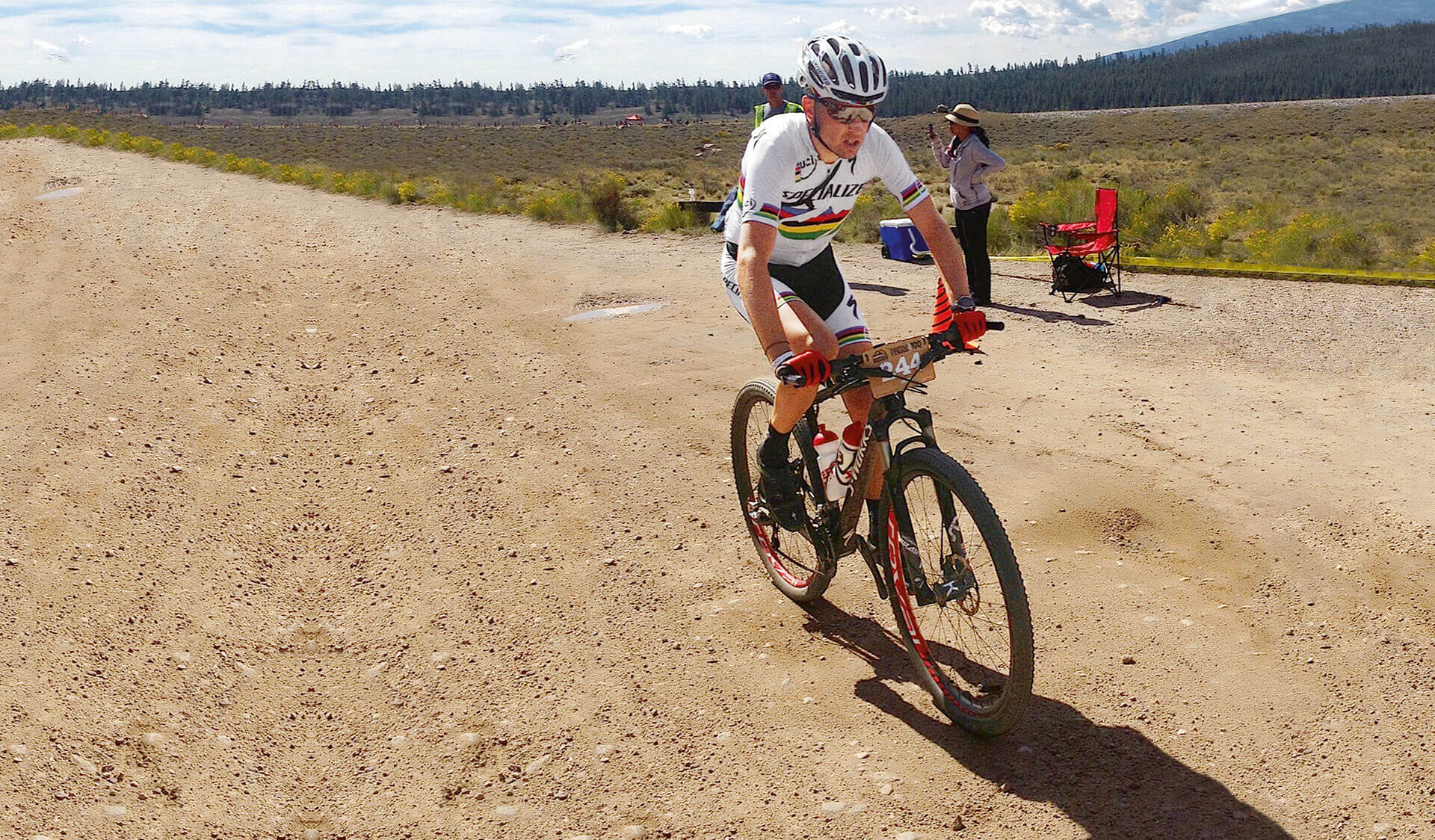
Innovations
Cyclists Take Additive Manufacturing for Hub and Drive a Spin
Kappius Components uses Additive Manufacturing for trailblazing bike hub/drive assembly. To American inventors, the “home garage” has always been a symbol of possibility – a place for tinkerers to create and innovate. More than acentury ago, the Wright brothers founded a cycle sales and repair business from a modest storefront and soon after invented a bike hub that was self-oiling. Everyone knows what they did next in the field of aviation.
And garage-based entrepreneurs are still at it in the 21st century. About four years ago, Russ Kappius – mountain-bike enthusiast, winner of six Masters racing titles, and a research geophysicist/software developer – worked out a design for a novel oversized hub and high-performance drive assembly that transfers more power from pedal to chain to wheel.
Challenge
First of all, Russ Kappius and his son Brady – engineer and pro mountainbike rider – tried technologies like water- jet cutting and wire electrical discharge machining (WEDM) to tweak the design of their hubs step by step. However, either the process was limited in its capacity to produce dimensionally accurate and complex parts or the produced parts did not meet the required specifications and had a fairly long turnaround time.
Kappius Components manufactures and distributes innovative hubs and bicycle components. The company is based in Littleton, Colorado (USA) and was founded by inventor Russell Kappius.
In late 2011 they discovered Direct Metal Laser Sintering (DMLS). This Additive Manufacturing technology met their rapid turnaround needs and enabled them to produce parts to exacting specifications and with additional design complexity.
Solution
The beauty of the lightweight-yet-durable hub comes from the handmade sleek carbon-fiber shell, as well as the drive assembly housed inside it. The assembly is comprised of three major parts: an outer drive ring, an inner ring with 60 teeth, and eight pawls, which engage in pairs with the teeth on the inner ring. This setup functions like a ratchet allowing forward motion while preventing backward motion.
The technological advance in the system comes from two developments: the oversized design – it’s about twice the current standard diameter – and many more points of engagement. While the most standard drive trains have 18 to 36 points of engagement, the Kappius hub is built around a drivetrain with 240 points of engagement. So the pedal can engage every one-and-a-half degrees and give the rider an extra quarter- or half-pedal stroke. These features allow a cyclist to translate the act of pedaling into increased drive force which is great for racing and highly technical riding. “Our drive assembly is a critical innovation,” explains Kappius.

The Kappius rear hub is a groundbreaking lightweight, durable, oversized design. The components are all manufactured from an extremely durable tool steel using Direct Metal Laser Sintering (DMLS). Source: Kappius Components
With DMLS Russ Kappius was able to redesign the pawl itself and add a 1-mm cylindrical basal extension. This positioned them better when they engaged. The Additive Manufacturing technology “grows” parts, according to a 3D digital model, layer by layer in a bed of powder. A focussed laser beam fuses the powder by following the contours and inside area of the part‘s cross-sectional slice. Once one layer has been completed, the powder bed is lowered by a few micrometres and the process begins again. Following the run, the parts are removed from the machine. On a CNC mill, the manufacturing support structures are removed and an extra 20-thousandths of material from the back side of the part is planed down. This creates a machined finish. Afterwards, the components are moved to a kiln and hardened to a value of 52 Rockwell C. The final assembly is done by the father-son team in their home shop.
Results
For two years, Russ and Brady Kappius field-tested additive manufactured versions of their hub and tweaked its design. In the first week of field testing, the elder Kappius won a race using the latest hub assembly. “We went from concept to bike-ready components in about a month,” enthuses the sportsman. “I’ve never been able to move that quickly before.“
Kappius Components’ hubs have been through several design iterations since the “garage doors” opened for business in 2008. The move to Additive Manufacturing has accelerated the speed of improvements. “DMLS has freed us up to make improvements on all of the elements in the system,” says the elder Kappius enthusiastically. In addition, the technology has also helped level the playing field between the two-person company and the bigger players in the bicycle industry. “Because we’re a startup, we quickly learned that we needed to make design changes and get new parts out to our customers fast,” remembers Russ Kappius. “We had to leverage our time to market to stay competitive.”

Swiss-born cyclist, Christoph Sauser, the 2012 crosscountry world champion, is shown riding Kappius hubs at “The Leadville 100” marathon mountain-bike race (Leadville, CO) in August 2012. He placed second in this race and later in the year won the Swiss national title, also using the innovative hub design. Source: Kappius Components
A typical order of ten drivetrain assemblies requires two builds on an EOSINT M 270. With the help of software the components can be arranged on the machine’s build platform to maximize output: ten outer rings, ten inner rings, and 80 pawls (eight for each assembly), plus a few extras. Run time is around 25 hrs. per plate, or 50 hrs. total for ten assemblies. Production is accelerating fast for the young company. In 2012 they sold about 100 hub assemblies and are projecting sales of 500 in 2014. The hub is shipped out to early-adopter cyclists around the world.
Since durability was of prime importance for the application, Kappius selected maraging steel from the available materials. The heat-treatable metal is characterized by excellent hardness and strength properties. Russ Kappius is pleased with the results. “The tool steel is super strong,” he says. “I haven’t had a single hub failure. Even the big manufacturers can’t say that.”
Last but not least the bike-hub creator summarizes the benefits of DMLS: “The essential asset is design freedom. Number two is the material strength closely followed by the lead time.” And then there’s also the rider experience. “People just love the hub,” says Russ Kappius. “They’re faster and fun to ride.”
“As a software engineer, I am able to change anything at any time to make the code better. With DMLS, I have similar flexibility. It allows me to make small design changes and almost immediately test them on the bike. That’s the beauty of the technology.” “DMLS has freed us up to make improvements on all of the elements in the system. Our drive assembly is a critical innovation.” Russ Kappius, inventor and founder of Kappius Components.
Contact
Arno Held
Business Development Manager
Lifestyle
EOS GmbH –Electro Optical Systems
Krailling/Munich, Germany
Phone +49 89 893 36-0
Send e-mail