
News
Measurement and Monitoring: Resources Assessment on Machine Tools
Sustainable benign manufacturing does not conflict with economic, social and environmental goals. On the contrary, research activities of today aim for environmental improvements are in line with economic benefits. How big is the improvement potential? Where and how can energy efficiency improvement or Eco design be applied?
While monitoring systems for machining process control are widely used and approved in manufacturing, e.g. with regard to tool breakage monitoring or preventive maintenance, systems for monitoring energy and resources are mostly neglected. In many cases there is no definition that clearly explains what monitoring systems are and what their abilities and defined benefits are. With monitoring the aim is a continuous and detailed assessment of the entire machine tool that helps to maintain or reach a defined energetic optimum, whereas selective measurements represent a current machine tool energetic behaviour and can indicate the individual potential.
The Institute of Machine Tools and Manufacturing (IWF) of the Federal Institute of Technology in Zurich focuses on a multichannel measurement for the full machine tool detail down to the component level on both measurement and monitoring. The measurement is not only limited to quantifying the effective power for electrical consumers, if needed, it can consider the compressed air flow, cooling flow and heat exchange within the machine tool system boundaries as defined in ISO DIS 14955-1.

Four steps to measure and monitor energy efficiency. power [P] for electrical consumers // compressed air flow [l/min] // cooling flow [l/min] // heat exchange [K]. Pictures: ETH
Selective power analyzers, which are currently used in other approaches, can have advantages in accuracy, resolution, and the variety of measured parameters and represent the right solution for assessing the network quality. For an application on overall machine tool component optimization this selective measurement and revealed information remains insufficient. A major challenge in the measurement and in monitoring is not only the amount of energy used in each component, but also its energetic behavior and control mode or interaction with other machine tool components. For this reason selective measurement approaches either have to ensure a constant machine tool state, use at least two measurement channels, or use smart analyzing algorithms in order to assure an adequate quantification for the machine tool and component interrelation. A combination of and synchronization with other energy forms, e.g. compressed air with effective power, can be quite challenging with selective measurements if applied on various machine tool systems within the industrial environment.
The current custom-designed multi-channel measurement system covers the requirements for the wide variety of machine tools, the types and number of channels, sampling rate and resolution, as well as used energy forms. In order to enable this detail level in monitoring applications as well, the IWF transformed the above mentioned features of the multichannel measurement system into a machine tool monitoring system. One of the major obstacles for the application of monitoring systems – the cost to benefit ratio – could be solved through the combination of different sensor sources (internal and external) with simulations to guarantee the full energetic machine tool behaviour with a minimum on investment.

Picture: ETH
The main advantages of monitoring systems are obvious: awareness, improvement indication, the relation to MES and ERP systems, long-term service and maintenance features or even realtime adaptive control possibilities are underestimated and reveal a justifiable potential. Therefore, in addition to statutory requirements, monitoring systems reveal improvement potential on both machine tool- and infrastructural-based micro-optimization and the production- and factory-related macro-optimization.
On the grounds of longtime experience in the machine tool energy- and resource-measurements with the self-developed measurement system, hard- and software, the IWF and the arising spin-off (Sigmatools) have developed an easy and individually applicable strategy for selective measurements and the implementation of monitoring systems including analysis functionalities.
Contact
Adam M. Gontarz
Research Engineer
ETH IWF Zürich
PFA E93
Zurich, Suisse
Phone +41 44 632 94 79
Send e-mail
www.cnczone.com
Advertisement
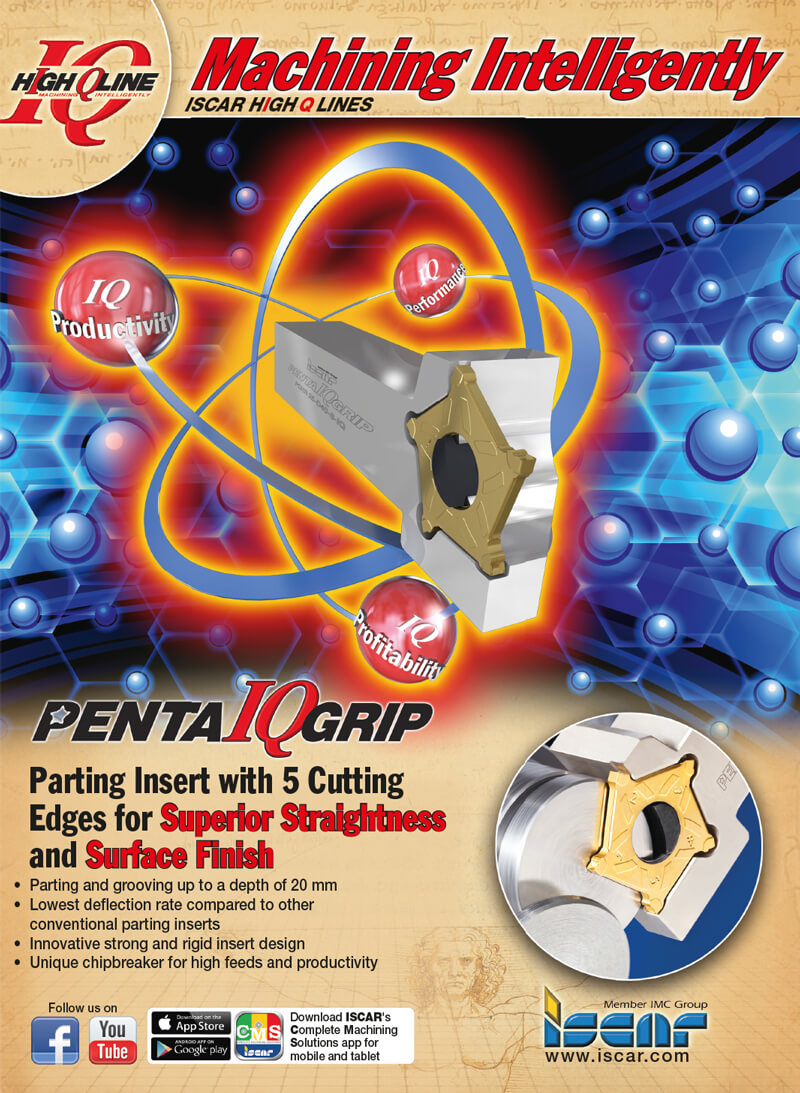