Innovate Manufactoring
Making light work of it: enhanced dynamics with CFRP
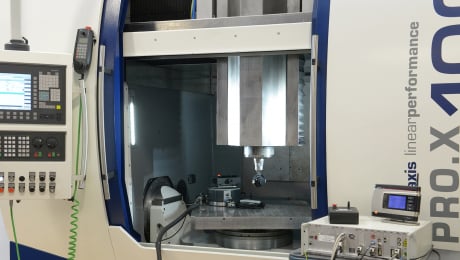
EMO Hannover 2017 provides inspiring ideas for lightweight construction
Frankfurt am Main, 03 May 2017. – Ultra-high-strength materials are highly popular not only in aircraft and automobile manufacturing, but also in the mechanical engineering sector, because they are often comparatively light and at the same time very sturdy. Machine tools, however, not infrequently come up against their physical limits when processing these materials. This can be remedied by using structural parts for machinery that are made of lightweight fibre-reinforced materials. This entails mastering some serious obstacles, as evidenced by an as-yet-uncompleted research project at the Fraunhofer Institute for Production Technology (IPT) in Aachen which will also be on show at the EMO Hannover.
CFRP replaces steel for enhanced dynamics
The researchers in Aachen usually adopt a holistic approach to optimising designs. In other words: they consider the machine’s design as a coherent whole, thus also including the development of important drive elements in the machine tool. They have currently joined forces with a machine tool manufacturer from Magdeburg to examine how an innovative machine component for vertical movements (Z-axis) made of carbon-fibre-reinforced plastic (CFRP) behaves in a machine tool and how the Z-slide can be optimised.
“We began development work on the CFRP slide in 2013,” relates Christoph Tischmann, Branch Manager of MAP Werkzeugmaschinen GmbH from Magdeburg. “We already possess plenty of experience with linear and rotary axes, for machining aluminium, for instance. But for high-strength materials like the titanium alloy Inconel they do not possess the requisite drive power.” So MAP decided to develop a machine tool with very powerful drives: for example, 55- and 72-kilowatt spindles (torque 210 and 273 Newtonmetres respectively in S1 or S6 mode) are now used, which are significantly heavier and larger. “So as not to have to compromise on the dynamics, we were looking for a way to compensate for the greater weight,” explains Christoph Tischmann. “That’s why we opted for the CFRP variant.” By way of comparison: the machine tool used to operate in the Z-axis with spindles rated at 28 to 36 kilowatts.
So what’s involved here is roughly doubling the drive power. At the same time, using CFRP reduces the mass by around 60 per cent compared to an axle made of steel. “However, we’re not aiming for any particular weight, we’re targeting an optimum ratio between weight and mechanical strength,” explains Filippos Tzanetos from the scientific staff of the Fraunhofer IPT.
The question arises here of how the change-over from a steel guide slide to a CFRP design with a drive weighing around twice as much will affect the design as a whole. The Fraunhofer IPT has for this purpose analysed the thermal and dynamic reactions of the entire machine on the Z-guide slides. “The machine was subjected to an exhaustive scrutiny,” reports Christoph Tischmann. “We used these measurements to develop several solutional approaches, in order to improve the design.”
The entire design is modified to suit the new material
Because materials cannot be simply replaced on a one-for-one basis, the design needs to be modified to suit the new material concerned. Finite-element simulation has proved its practical worth in this context. “At the computer, we take a detailed look at the specific points in the design that are the most yielding, in order to determine the causes involved,” explains Filippos Tzanetos. “We then attempt to replace some of the existing components by their equivalents in aluminium or CFRP, or to improve the dynamic behaviour at certain critical points by means of reinforcements or ribs.”
In projects of this kind, the Fraunhofer Institute is often assisted by other institutes or spin-offs, but in this case the scientists found the support they needed in-house. “In our institute, we have a department for fibre-reinforced-composite and laser-system technologies”, reports Filippos Tzanetos. “This department has over the course of many years accumulated a lot of can-do competences in the field of dimensioning machine tool components made of fibre-reinforced plastics (FRPs), and provides us with proactive support in the shape of simulation expertise for fibre-reinforced component dimensioning.”
Success assured by synergised competences
Support of this kind is indispensable for solving questions encountered when it comes to using FRP components in plant and machinery construction, since these materials, by virtue of their anisotropic properties, are not often used here. “Up to now, there has been a notable reluctance to use FRPs because in contrast to conventional materials there is no recourse available to existing design and dimensioning standards and therefore it’s not that easy to predict an FRP component’s dynamic behaviour in conjunction with the rest of the machine’s structure,” explains the Aachen-based scientist. “Mistakes are made, for example, when a component is dimensioned in terms of its mechanical strength in just one axis direction, while ignoring the mechanical strength in the other axis directions. But if we use simulation tools to fine-tune the interrelationship between the FRP component and the machine tool’s own dynamics, nothing can go wrong. So to solve the problem, the requisite competences are brought together in our company within this project.”
Lasering, not bonding
Another critical consideration is joining CFRPs to metals. Up to now, an adhesive bonding process has been used, which according to Filippos Tzanetos has four disadvantages:
- The CFRP surface has to be machined mechanically. This leads to unsteadiness and a weakening of the CFRP’s properties.
- It guarantees only a low level of mechanical strength (per joint: 10 to 40 megapascal).
- It is closely dependent on the ambient conditions (e.g. temperature, soiling, chips, cooling lubricant).
- Bonded joints possess a low resistance to wear.
All these disadvantages are eliminated by a lasering process. But it’s not only the joining technology that MAP’s Branch Manager sees as problematic. “In order to assure precise positioning and reproducibility accuracies in the machine even in the case of high dynamic response, we scrape off the layers on the linear guides by hand,” says Christoph Tischmann. “It’s now an enormous challenge for us to accomplish this with CFRPs as well.”
Despite all these difficulties, the change-over to CFRP has been worth it, opines the expert with a view to the EMO Hannover. The machine tool manufacturer is thinking about a shared information stand with the Fraunhofer IPT, in order to showcase the advances and procedures involved with this “new material”. “Basically, at the end of this project we aim to be putting a dynamic, high-precision, and above all powerful machine on the market,” explains Christoph Tischmann. “We would like to see it becoming widely accepted in the aerospace sector, particularly.”
EMO Hannover is also inspiring the academic community
The IPT scientist, too, sees collaborative projects like that with MAP Werkzeugmaschinen GmbH as a good option for exploring new paths in a process of mutual feedback with the industrial sector. The project currently ongoing has encouraged the researchers in Aachen to press ahead with industrial partners in the field of CFRPs. Filippos Tzanetos and his colleagues from the academic community will be getting further input on comparable material-related questions and on lightweight construction in September at the EMO Hannover.
Profiles
Fraunhofer IPT, Aachen
The Fraunhofer IPT develops system solutions for production. We focus on the topics of process technology, production machines, production quality and metrology as well as technology management. Our clients and cooperation partners represent all fields of industry: from aerospace technology to the automotive industry and its suppliers as well as tool and die making companies and the precision mechanics, optics and machine tool industries in particular.
Operating budget in 2016: around 27.9 million euros; employees: 450
MAP Werkzeugmaschinen GmbH, Magdeburg
In 1995, MAP was founded by expert staff from the former Fritz Werner Werkzeugmaschinen GmbH. MAP is currently responsible for design, both electrical and mechanical, manufacture, service support and spindle service. Synergetic effects are also created by the firm’s sales partner Lerinc Werkzeugmaschinen & Automation GmbH from Heiligenhaus, which handles both sales and the administrative work involved. The present-day MAP Werkzeugmaschinen GmbH scores highly not only in terms of corporate expertise and professional competence in the above-mentioned fields, but also with its many years of intensive sectoral experience in mechanical engineering and the metal-cutting industry. Which is why it meanwhile possesses a prestigious customer base, not least in the automotive and aerospace sectors. Employees: 16
Author: Nikolaus Fecht, specialist journalist from Gelsenkirchen (9,613 characters incl. blanks)
Your contact persons
Fraunhofer Institute for Production Technology IPT
Susanne Krause
External and internal communication
Steinbachstrasse 17
52074 Aachen
Germany
Phone +49 241 8904-180
[email protected]
www.ipt.fraunhofer.de
MAP Werkzeugmaschinen GmbH
Christoph Tischmann
Branch Manager
Alt Salbke 6 – 10
39122 Magdeburg
Germany
Phone +49 391 4080715
[email protected]
www.map-wzm.de
EMO Hannover 2017 – the world’s premier trade fair for the metalworking sector
From 18 to 23 September 2017, international manufacturers of production technology will be spotlighting “Connecting systems for intelligent production” at the EMO Hannover 2017. The world’s premier trade fair for the metalworking industry will be showcasing the entire bandwidth of today’s most sophisticated metalworking technology, which is the heart of every industrial production process. The fair will be presenting the latest machines, plus efficient technical solutions, product-supportive services, sustainability in the production process, and much, much more. The principal focus of the EMO Hannover is on metal-cutting and forming machine tools, production systems, high-precision tools, automated material flows, computer technology, industrial electronics and accessories. The trade visitors to the EMO come from all major sectors of industry, such as machinery and plant manufacturers, the automotive industry and its component suppliers, the aerospace sector, precision mechanics and optics, shipbuilding, medical technology, tool and die manufacture, steel and lightweight construction. The EMO Hannover is the world’s most important international meeting point for production technology specialists from all over the planet. In 2013, the fair attracted more than 2,130 exhibitors, and around 143,000 trade visitors from more than 100 different countries. EMO is a registered trademark of the European Association of the Machine Tool Industries CECIMO.
You will find texts and images relating to the EMO Hannover 2017 on the internet under
www.emo-hannover.de/en/press/press-releases/press-releases/press-releases.xhtml
in the Press section. You can also follow the EMO Hannover using our social media channels
http://twitter.com/EMO_HANNOVER
https://de.industryarena.com/emo-hannover
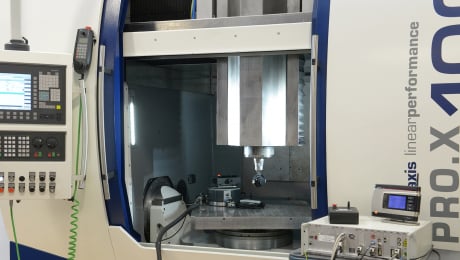
EMO Hannover 2017 provides inspiring ideas for lightweight construction
Frankfurt am Main, 03 May 2017. – Ultra-high-strength materials are highly popular not only in aircraft and automobile manufacturing, but also in the mechanical engineering sector, because they are often comparatively light and at the same time very sturdy. Machine tools, however, not infrequently come up against their physical limits when processing these materials. This can be remedied by using structural parts for machinery that are made of lightweight fibre-reinforced materials. This entails mastering some serious obstacles, as evidenced by an as-yet-uncompleted research project at the Fraunhofer Institute for Production Technology (IPT) in Aachen which will also be on show at the EMO Hannover.
CFRP replaces steel for enhanced dynamics
The researchers in Aachen usually adopt a holistic approach to optimising designs. In other words: they consider the machine’s design as a coherent whole, thus also including the development of important drive elements in the machine tool. They have currently joined forces with a machine tool manufacturer from Magdeburg to examine how an innovative machine component for vertical movements (Z-axis) made of carbon-fibre-reinforced plastic (CFRP) behaves in a machine tool and how the Z-slide can be optimised.
“We began development work on the CFRP slide in 2013,” relates Christoph Tischmann, Branch Manager of MAP Werkzeugmaschinen GmbH from Magdeburg. “We already possess plenty of experience with linear and rotary axes, for machining aluminium, for instance. But for high-strength materials like the titanium alloy Inconel they do not possess the requisite drive power.” So MAP decided to develop a machine tool with very powerful drives: for example, 55- and 72-kilowatt spindles (torque 210 and 273 Newtonmetres respectively in S1 or S6 mode) are now used, which are significantly heavier and larger. “So as not to have to compromise on the dynamics, we were looking for a way to compensate for the greater weight,” explains Christoph Tischmann. “That’s why we opted for the CFRP variant.” By way of comparison: the machine tool used to operate in the Z-axis with spindles rated at 28 to 36 kilowatts.
So what’s involved here is roughly doubling the drive power. At the same time, using CFRP reduces the mass by around 60 per cent compared to an axle made of steel. “However, we’re not aiming for any particular weight, we’re targeting an optimum ratio between weight and mechanical strength,” explains Filippos Tzanetos from the scientific staff of the Fraunhofer IPT.
The question arises here of how the change-over from a steel guide slide to a CFRP design with a drive weighing around twice as much will affect the design as a whole. The Fraunhofer IPT has for this purpose analysed the thermal and dynamic reactions of the entire machine on the Z-guide slides. “The machine was subjected to an exhaustive scrutiny,” reports Christoph Tischmann. “We used these measurements to develop several solutional approaches, in order to improve the design.”
The entire design is modified to suit the new material
Because materials cannot be simply replaced on a one-for-one basis, the design needs to be modified to suit the new material concerned. Finite-element simulation has proved its practical worth in this context. “At the computer, we take a detailed look at the specific points in the design that are the most yielding, in order to determine the causes involved,” explains Filippos Tzanetos. “We then attempt to replace some of the existing components by their equivalents in aluminium or CFRP, or to improve the dynamic behaviour at certain critical points by means of reinforcements or ribs.”
In projects of this kind, the Fraunhofer Institute is often assisted by other institutes or spin-offs, but in this case the scientists found the support they needed in-house. “In our institute, we have a department for fibre-reinforced-composite and laser-system technologies”, reports Filippos Tzanetos. “This department has over the course of many years accumulated a lot of can-do competences in the field of dimensioning machine tool components made of fibre-reinforced plastics (FRPs), and provides us with proactive support in the shape of simulation expertise for fibre-reinforced component dimensioning.”
Success assured by synergised competences
Support of this kind is indispensable for solving questions encountered when it comes to using FRP components in plant and machinery construction, since these materials, by virtue of their anisotropic properties, are not often used here. “Up to now, there has been a notable reluctance to use FRPs because in contrast to conventional materials there is no recourse available to existing design and dimensioning standards and therefore it’s not that easy to predict an FRP component’s dynamic behaviour in conjunction with the rest of the machine’s structure,” explains the Aachen-based scientist. “Mistakes are made, for example, when a component is dimensioned in terms of its mechanical strength in just one axis direction, while ignoring the mechanical strength in the other axis directions. But if we use simulation tools to fine-tune the interrelationship between the FRP component and the machine tool’s own dynamics, nothing can go wrong. So to solve the problem, the requisite competences are brought together in our company within this project.”
Lasering, not bonding
Another critical consideration is joining CFRPs to metals. Up to now, an adhesive bonding process has been used, which according to Filippos Tzanetos has four disadvantages:
- The CFRP surface has to be machined mechanically. This leads to unsteadiness and a weakening of the CFRP’s properties.
- It guarantees only a low level of mechanical strength (per joint: 10 to 40 megapascal).
- It is closely dependent on the ambient conditions (e.g. temperature, soiling, chips, cooling lubricant).
- Bonded joints possess a low resistance to wear.
All these disadvantages are eliminated by a lasering process. But it’s not only the joining technology that MAP’s Branch Manager sees as problematic. “In order to assure precise positioning and reproducibility accuracies in the machine even in the case of high dynamic response, we scrape off the layers on the linear guides by hand,” says Christoph Tischmann. “It’s now an enormous challenge for us to accomplish this with CFRPs as well.”
Despite all these difficulties, the change-over to CFRP has been worth it, opines the expert with a view to the EMO Hannover. The machine tool manufacturer is thinking about a shared information stand with the Fraunhofer IPT, in order to showcase the advances and procedures involved with this “new material”. “Basically, at the end of this project we aim to be putting a dynamic, high-precision, and above all powerful machine on the market,” explains Christoph Tischmann. “We would like to see it becoming widely accepted in the aerospace sector, particularly.”
EMO Hannover is also inspiring the academic community
The IPT scientist, too, sees collaborative projects like that with MAP Werkzeugmaschinen GmbH as a good option for exploring new paths in a process of mutual feedback with the industrial sector. The project currently ongoing has encouraged the researchers in Aachen to press ahead with industrial partners in the field of CFRPs. Filippos Tzanetos and his colleagues from the academic community will be getting further input on comparable material-related questions and on lightweight construction in September at the EMO Hannover.
Profiles
Fraunhofer IPT, Aachen
The Fraunhofer IPT develops system solutions for production. We focus on the topics of process technology, production machines, production quality and metrology as well as technology management. Our clients and cooperation partners represent all fields of industry: from aerospace technology to the automotive industry and its suppliers as well as tool and die making companies and the precision mechanics, optics and machine tool industries in particular.
Operating budget in 2016: around 27.9 million euros; employees: 450
MAP Werkzeugmaschinen GmbH, Magdeburg
In 1995, MAP was founded by expert staff from the former Fritz Werner Werkzeugmaschinen GmbH. MAP is currently responsible for design, both electrical and mechanical, manufacture, service support and spindle service. Synergetic effects are also created by the firm’s sales partner Lerinc Werkzeugmaschinen & Automation GmbH from Heiligenhaus, which handles both sales and the administrative work involved. The present-day MAP Werkzeugmaschinen GmbH scores highly not only in terms of corporate expertise and professional competence in the above-mentioned fields, but also with its many years of intensive sectoral experience in mechanical engineering and the metal-cutting industry. Which is why it meanwhile possesses a prestigious customer base, not least in the automotive and aerospace sectors. Employees: 16
Author: Nikolaus Fecht, specialist journalist from Gelsenkirchen (9,613 characters incl. blanks)
Your contact persons
Fraunhofer Institute for Production Technology IPT
Susanne Krause
External and internal communication
Steinbachstrasse 17
52074 Aachen
Germany
Phone +49 241 8904-180
[email protected]
www.ipt.fraunhofer.de
MAP Werkzeugmaschinen GmbH
Christoph Tischmann
Branch Manager
Alt Salbke 6 – 10
39122 Magdeburg
Germany
Phone +49 391 4080715
[email protected]
www.map-wzm.de
EMO Hannover 2017 – the world’s premier trade fair for the metalworking sector
From 18 to 23 September 2017, international manufacturers of production technology will be spotlighting “Connecting systems for intelligent production” at the EMO Hannover 2017. The world’s premier trade fair for the metalworking industry will be showcasing the entire bandwidth of today’s most sophisticated metalworking technology, which is the heart of every industrial production process. The fair will be presenting the latest machines, plus efficient technical solutions, product-supportive services, sustainability in the production process, and much, much more. The principal focus of the EMO Hannover is on metal-cutting and forming machine tools, production systems, high-precision tools, automated material flows, computer technology, industrial electronics and accessories. The trade visitors to the EMO come from all major sectors of industry, such as machinery and plant manufacturers, the automotive industry and its component suppliers, the aerospace sector, precision mechanics and optics, shipbuilding, medical technology, tool and die manufacture, steel and lightweight construction. The EMO Hannover is the world’s most important international meeting point for production technology specialists from all over the planet. In 2013, the fair attracted more than 2,130 exhibitors, and around 143,000 trade visitors from more than 100 different countries. EMO is a registered trademark of the European Association of the Machine Tool Industries CECIMO.
You will find texts and images relating to the EMO Hannover 2017 on the internet under
www.emo-hannover.de/en/press/press-releases/press-releases/press-releases.xhtml
in the Press section. You can also follow the EMO Hannover using our social media channels
http://twitter.com/EMO_HANNOVER
https://de.industryarena.com/emo-hannover