igus expands additive production offering with second laser sintering material
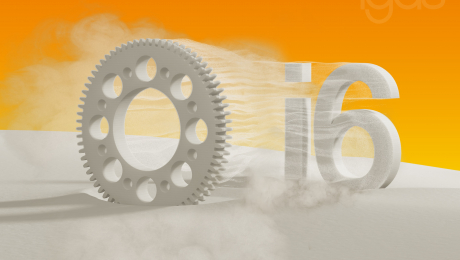
The motion plastics specialist igus has expanded its 3D print range with a new selective laser sintering (SLS) material that is particularly suitable for the additive manufacture of gear wheels. Characterised by a wear resistance of at least six times that of standard materials, the iglidur i6 material is well-suited for printing wear resistant parts, such as gears, offering a particularly long service life.
“Today, additive manufacturing is becoming an important topic in the industry,” says Robert Dumayne, dry-tech director, igus. “This is mainly due to the fact that special parts can be printed easily, cost-effectively and quickly from individual parts up to medium size batches. The new iglidur i6 material expands the existing range of six tribofilaments for the fused deposition modelling (FDM) method and iglidur i3 for the SLS process.”
At the company’s in-house 2,750 m² test lab, a 3D printed gear wheel, made of iglidur i6, was put through its paces to exemplify its high wear resistance properties. In the test a worm wheel drive with 5 Nm torque and 12 rpm was used, and gears made from different materials compared. The SLS printed PA12 gear failed after 521 cycles, as the heat generated by friction melted the plastic. The gear made of iglidur i3 stopped at around 345,000 cycles. The iglidur i6 gear was still fully functional after 1 million cycles, showing only minor wear.
The iglidur i6 gear was also compared with machined gears. The gear made of POM (Polyoxymethylene) failed after 621,000 cycles, while the machined PBT (Polybutylene Terephthalate) gear stopped working after 155,000 cycles.
Via its 3D printing service, www.igus.co.uk/3dprintservice, simply upload the STEP file and select the new SLS iglidur i6 material. With a mouse click, the customer can order printed parts for shipment within 1-3 days, or request a quotation. For more information from igus, please visit: www.igus.co.uk or call igus directly on 01604 677240.
About igus
Based in Northampton in the UK and with global headquarters in Cologne, Germany, igus is a leading international manufacturer of energy chain systems and polymer plain bearings. The family-run company is represented in 35 countries and employs approximately 3,000 people worldwide. In 2016, igus achieved sales of 592 million euros with motion plastics, plastic components for moving applications.
With plastic bearing experience since 1964, cable carrier experience since 1971 and continuous-flex cable since 1989, igus provides the right solution based on 100,000 products available from stock with between 1,500 and 2,500 new product introductions each year. igus operates the largest test laboratories and factories in its sector to offer customers quick turnaround times on innovative products and solutions tailored to their needs.
The terms igus, chainflex, CFRIP, conprotect, CTD, drylin, dry-tech, dryspin, easy chain, e-chain, e-chain systems, e-ketten, e-kettensysteme, e-skin, energy chain, energy chain systems, flizz, iglide, iglidur, igubal, invis, manus, motion plastics, pikchain, readychain, readycable, speedigus, triflex, twisterchain, plastics for longer life, robolink, xiros, xirodur and vector are protected by trademark laws in the Federal Republic of Germany and internationally, where applicable.
All other registered trademarks and trademarks are the property of their respective owners.
For further information, please contact:
Megan Campbell, igus
Tel: 01604 677240
Email: [email protected]
Sumbul Baig, Technical Publicity
Tel: 01582 390980
Email: [email protected]
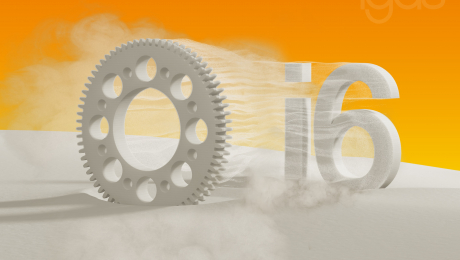
The motion plastics specialist igus has expanded its 3D print range with a new selective laser sintering (SLS) material that is particularly suitable for the additive manufacture of gear wheels. Characterised by a wear resistance of at least six times that of standard materials, the iglidur i6 material is well-suited for printing wear resistant parts, such as gears, offering a particularly long service life.
“Today, additive manufacturing is becoming an important topic in the industry,” says Robert Dumayne, dry-tech director, igus. “This is mainly due to the fact that special parts can be printed easily, cost-effectively and quickly from individual parts up to medium size batches. The new iglidur i6 material expands the existing range of six tribofilaments for the fused deposition modelling (FDM) method and iglidur i3 for the SLS process.”
At the company’s in-house 2,750 m² test lab, a 3D printed gear wheel, made of iglidur i6, was put through its paces to exemplify its high wear resistance properties. In the test a worm wheel drive with 5 Nm torque and 12 rpm was used, and gears made from different materials compared. The SLS printed PA12 gear failed after 521 cycles, as the heat generated by friction melted the plastic. The gear made of iglidur i3 stopped at around 345,000 cycles. The iglidur i6 gear was still fully functional after 1 million cycles, showing only minor wear.
The iglidur i6 gear was also compared with machined gears. The gear made of POM (Polyoxymethylene) failed after 621,000 cycles, while the machined PBT (Polybutylene Terephthalate) gear stopped working after 155,000 cycles.
Via its 3D printing service, www.igus.co.uk/3dprintservice, simply upload the STEP file and select the new SLS iglidur i6 material. With a mouse click, the customer can order printed parts for shipment within 1-3 days, or request a quotation. For more information from igus, please visit: www.igus.co.uk or call igus directly on 01604 677240.
About igus
Based in Northampton in the UK and with global headquarters in Cologne, Germany, igus is a leading international manufacturer of energy chain systems and polymer plain bearings. The family-run company is represented in 35 countries and employs approximately 3,000 people worldwide. In 2016, igus achieved sales of 592 million euros with motion plastics, plastic components for moving applications.
With plastic bearing experience since 1964, cable carrier experience since 1971 and continuous-flex cable since 1989, igus provides the right solution based on 100,000 products available from stock with between 1,500 and 2,500 new product introductions each year. igus operates the largest test laboratories and factories in its sector to offer customers quick turnaround times on innovative products and solutions tailored to their needs.
The terms igus, chainflex, CFRIP, conprotect, CTD, drylin, dry-tech, dryspin, easy chain, e-chain, e-chain systems, e-ketten, e-kettensysteme, e-skin, energy chain, energy chain systems, flizz, iglide, iglidur, igubal, invis, manus, motion plastics, pikchain, readychain, readycable, speedigus, triflex, twisterchain, plastics for longer life, robolink, xiros, xirodur and vector are protected by trademark laws in the Federal Republic of Germany and internationally, where applicable.
All other registered trademarks and trademarks are the property of their respective owners.
For further information, please contact:
Megan Campbell, igus
Tel: 01604 677240
Email: [email protected]
Sumbul Baig, Technical Publicity
Tel: 01582 390980
Email: [email protected]