Diamond tools cut CFRP cleanly and efficiently
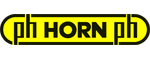

“Once you've stood on a virus board, you will realise that these boards are addictive”, jokes Frank Dietzel. The Managing Director of Virus Sportartikel GmbH has been producing high-end snowboards and skis for highly discerning winter sports enthusiasts at his workshop for more than 30 years. Together with his team, Dietzel relies on high-tech fibre composite materials and native timber to manufacture these products. “Each of our boards contains a flexible wood core”, explains Dietzel. As well as requiring lots of manual work, the processes of cutting the CFRP mats and milling the wood cores also involve using a CNC milling machine. For this, the company's specialists rely on diamond tools from Tübingen-based Paul Horn GmbH.
Back in 1984 when the sport of snowboarding was still very much in its infancy, Dietzel started professionally producing this new type of winter sports equipment in Großwallstadt, Bavaria. Since then, the Virus brand has become a stalwart of the industry. Professionals and discerning winter sports enthusiasts count on the performance of its skis and snowboards. Virus boards are made by sandwiching together high-tech materials and solid wood cores. The wood cores are made completely by hand and, depending on the model, reinforced with two or three carbon fibre inserts. For his top models, Dietzel also uses a material called Zylon, which is the strongest man-made fibre ever produced. “Zylon is like a synthetic spider thread that is much more resistant to tearing than carbon. Processing this material is very complex and you need special tools and technologies just to be able to cut the fibres”, says Dietzel.
The individual layers of the sandwich structure are responsible for different tasks. The core determines most of the properties exhibited by the finished board. Wood is a good choice of core material because of its all-round characteristics. Each wood core is made from several strips of laminated hardwood that are stuck together. These provide the board with natural flexibility and have good vibration-damping properties. To reinforce specific areas of the board, carbon and fibreglass inserts are placed inside the laminate. The equipment has to adapt to the ground during rapid turns (carving), but must also quickly bend back into its original shape when the load changes. The important thing here is that the material must not behave like a coiled spring, as this would have a major impact on board control. Dietzel laminates CFRP mats into the core and the outer layer, which boosts board handling and performance even further.
CVD diamond
For cutting the CFRP mats and milling the wood cores, Dietzel relies on CVD diamond-tipped and CVD diamond-coated milling tools from HORN as well as on a CNC portal milling machine. “The materials are very abrasive. Carbide would wear away too quickly during machining”, explains HORN field sales representative Stefan Bachmann. The CFRP mats and the 3D shapes of the wood cores are milled using DSS diamond-coated end mills. The edges are trimmed with a CVD-D-tipped milling cutter with five cutting edges.
“The edges of the CFRP mats are very important. If any parts are frayed or delaminated, they are useless. We are completely satisfied with the performance of HORN milling tools, because rejects are very costly when you are using CFRP”, explains Dietzel. Prior to milling, an additional fabric is stuck onto the CFRP mats to protect the edges. This fabric is removed after machining. For the milling operations, Dietzel uses a CNC portal milling machine, which would normally be used in the woodworking industry to produce furniture parts. “With its vacuum clamping table, the machine provides us with all the features and machining options that we need for our products”, clarifies the Managing Director.
Cutting rather than crushing
CVD diamond differs from PCD diamond cutting edges in several ways. CVD diamond is 99.99 per cent pure diamond – in contrast to PCD, which is mixed with a binder that makes up 10 to 20 per cent. Although both cutting materials are polycrystalline, CVD diamond has a more homogeneous structure that is almost as hard and wear-resistant as natural monocrystalline diamond. Whereas PCD cutting edges are usually ground or eroded, CVD cutting edges are precision-lasered. As a result, the cutting edge roundness of between one and two microns makes them at least ten times as sharp. During PCD grinding, boundary crystals at the cutting edge are knocked out but during CVD diamond laser cutting, the beam slices through them. This also explains the long tool life that is achieved when machining carbon-fibre and glass-fibre reinforced plastics. With their sharpness of 1 to 2 µm, CVD diamond cutting edges slice through thin fibres measuring 5 to 8 µm in thickness whereas PCD cutting edges are ten times blunter meaning that they merely crush the fibres and wear away more quickly due to friction.