Tool by tool – Tooth by tooth
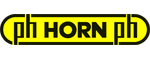

Over recent years, HORN has been constantly expanding its portfolio of tools for cost-effective gear production. The choice of tool solution depends on various factors. The key ones that determine which manufacturing technology is selected are: the module, the batch sizes involved and the existing machine technology. HORN has developed productive tool solutions to accommodate the different applications. In particular, new machine tools with synchronised axes now offer the kinds of gear tooth production capabilities that were previously the preserve of special machines. Within this context, HORN is not just there for you as a tool supplier, but as a partner for developing new production strategies directly at the machine. Designing a tool also involves defining the machining parameters and configuring the machine tool settings. These are supplied by HORN together with the tool. Preparation of the tooth cutting tools is a fundamental aspect when considering the cost per part.
Gear milling with the HORN circular milling system
For one customer, the process of optimising an actuator gear manufacturing process resulted in huge time savings, low tool costs and increased accuracy. Before switching over to the circular milling system, the user had to cut the gear teeth with outdated tools on special gear cutting machines. This meant high set-up costs and long lead times. HORN’s proposed solution consisted of the 613 tool system for gear milling. The process solution met the desired requirements: complete machining in a single clamping, higher precision, improved tooth surface quality and the sought-after time savings. In spite of the high cutting pressure associated with the six teeth, the tools are extremely stable. The type 613 circular milling insert has a tool life of 1,000 workpieces. The involute profile of the cutting edges is precision-ground. The cutting speed is vc = 310 m/min (1,017 feet (ft)/min) and the feed rate is programmed to a value of 600 mm/min (23.622"/min). The tool mills each of the eight teeth per gear to the full depth of 2.1 mm (0.0827") in a single operation. A conventional milling direction is used.
Gear broaching with a broaching unit
When HORN optimised a serration broaching process, it resulted in a threefold improvement on more than one level: a tool life three times longer and a process time three times shorter. The user was already pleased with the performance of the HORN broaching tools they had been using so far. However, they needed to optimise the machining time in light of the large batch sizes involved. Up until that point, they had been using a conventional broaching method. In other words, a large number of individual strokes with an infeed of 0.1 mm were required to broach the tooth to the full depth. This resulted in a broaching process time of approximately three minutes for a total of eleven teeth. The HORN field sales force suggested switching from conventional broaching to the use of a broaching unit instead. The broaching unit is installed on the turret via the VDI interface. A cam is used to convert the rotary motion of the drive shaft into linear motion of the plunger. It enters the workpiece with the cutting edge and is lifted clear of the material by the integrated retraction device at the end of the broaching operation. The retraction device prevents the cutting edge from becoming worn or breaking off while it is being retracted from the workpiece. By the end of the initial trials, the revised broaching process had already proven itself. Those involved in the project were able to increase the life of the Supermini N105 broaching tool from 30 serrations to 100 serrations. The process time fell from three minutes to around one.
Five-axis milling of large modules
For sizes ranging from module 4 to 30, HORN offers gear cutting solutions for prototypes and small and medium-sized series on universal machining centres using standard tools, such as end mills, ball nose end mills, toroidal milling cutters, side milling cutters, cup wheel milling cutters and conical milling cutters from HORN’s standard range. Supported by the software, the standard tools are capable of producing every tooth profile geometry: spur gears with straight, helical or double-helical teeth; worm wheels; various bevel gears; and gear wheels such as Cyclo-Palloid gears. Rough milling is carried out using DGM, DSDS and DAH37-type high-feed milling cutters or the M279 system. Tooth form flanks and base profiles are machined using solid carbide end, torus and radius milling cutters from the DSM system. DGFF-type milling cutters take care of deburring and chamfering. Exchangeable head milling cutters from the DG system, specifically DGVZ milling cutters, are also used. Following hardening, standard milling cutters made of special carbide grades carry out the final machining. All of these are cost-effective standard milling cutters with short delivery times. As a result of all this, complex gear teeth can be produced on universal, five-axis turn-mill centres. This saves enormous amounts of time and money compared to producing them on expensive gear cutting machines. The universal machining centres allow the respective blank geometries to be produced first and then – in the same clamping process – gears for a variety of scenarios (single-part production, prototype applications, or small and medium-sized series), followed by parts of a completely different kind.
Gear skiving
HORN’s gear skiving product range is yet more testament to the company’s gear cutting expertise. The tool system encompasses products for the high-yield manufacturing of internal gears, splines and other internal profiles, as well as external gears with interfering edges. In these applications, the key advantages offered by gear skiving are: significantly shorter process times in comparison to tooth broaching, the ability to use the technique on optimised turn-mill centres, turning and gear cutting in one clamping, the absence of reliefs at the tooth end, a manufacturing process that is generally more productive and cost-effective than gear shaping and broaching, and cycle times that are four to five times shorter than for broaching processes. Gear skiving tools are designed for gear cutting in medium to large batches. With this method, HORN is able to offer the benefit of a shorter process time for larger modules, especially in the case of internal gear teeth. For gear skiving with larger modules, large and rigid milling and turning centres are required to facilitate proper synchronisation between the workpiece and tool spindles. Thanks to its experience with small gear skiving tools made of solid carbide, HORN has been able to apply this expertise to cover larger modules as well. HORN gear skiving tools are specially designed and constructed for every individual application. The feasibility of each application is verified by engineers prior to implementation and the tool design and recommendations for the process are discussed with the user.
Thread whirling
Thread whirling is a machining process in which the workpiece and the tool both rotate at a specific speed ratio. During this, the tool is positioned at a certain angle in relation to the workpiece. The important thing here is that the rotation of the workpiece spindle and tool must be linked. In addition to machining crown and spur gears, this method can also be used for the efficient production of involute teeth or splines. It is compatible with virtually all HORN milling systems. The advantage of the method is that fewer tool movements are required because all tooth spaces are created in one pass. The technique can be used on almost all turn-mill centres, making it suitable for universal use.