We are your MES partner!
Storage and transport – Useful added value in an MES context
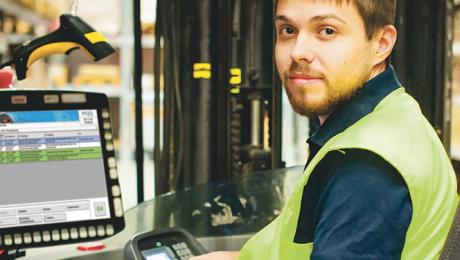
PROXIA Internal transport logistics
Storage and transport processes in companies can be very straightforward, but sometimes not! The heart of the lean philosophy is the prevention of waste in all company processes. As order numbers rise, the production process overview is quickly lost. With regard to storage and transport, questions arise such as where are the semi-finished goods kept, because we need complete the current step?
A high-tech MES system within an all-round LEAN concept can help answer this question.
The current production standard on the test bench
A specific example shows what is meant by “standard” in many companies today: An employee, let’s call him Mr Müller, walks through production with a clipboard. His task is to determine where semi-finished goods are located in production, to which production order they belong, and which machine should be used to process this order next. Production orders consist of a range of processing steps. If there is a large machine pool and a normally high number of production orders for the machines and plant, a lot of semi-finished goods are stockpiled, and it is extremely difficult to manage these efficiently and transparently using this method.
Therefore, no one in production, not even Mr Müller, has a complete overview of the storage and transport of semi-finished goods. As there are no defined storage areas, operators put the semi-finished goods wherever they can find space. Mostly they remain on the machine on which they have just been processed until they are required by the next step. If this is not immediately the case, or a very large volume has been produced, this machine can sometimes be put out of use due to lack of space. The responsible operators may also decide to make space to house the parts. In the worst case scenario, the operator leaves his work area to look for Mr Müller or a forklift driver who can help him transport the parts. As there are no defined storage areas, the operator puts the goods wherever there is space. He might then forget to record the storage location because, e.g. he takes a break. As a result, the machine is not only out of action, but Mr Müller is left with the task of finding the parts.
The main thrust of a lean philosophy, the prevention of waste in all company processes, is not applied in this example. Lean production applies this philosophy to production processes. The example described above includes many types of waste relating to the lean production concept, the most obvious being:
- Movement – Mr Müller spends the whole day in production, trying to find semi-finished goods
- Stock – Storage of semi-finished goods between processes in undefined locations
- Transport – Semi-finished goods appear to be kept and transported between processes without a defined plan
Production standard is now Industry 4.0 capable with MES
In order to reduce these types of waste to an absolute minimum, high-tech MES solutions not only support the planning and processing of production orders, but also support internal transport logistics within the lean philosophy concept. For example, production logistics, e.g. forklifts, can be directly linked to the MES system using an extended operator terminal. This enables the operator to request transport from the forklift driver direct from the BDE terminal without having to leave his work area. The relevant employee can also see exactly where the semi-finished goods he requires for the following process are located, therefore allowing “chaotic warehousing” in production. Only the temporary storage location of the specific semi-finished product needs to be recorded in the MES system. Everyone involved in the process can then see where the relevant material is located at any time.
Mr Müller in our example can now turn his attention to other tasks because searching for material is a thing of the past. The operator’s terminal shows the location of the required semi-finished goods or materials, whether they are on the machine used for the previous process, at storage location C22, shelf 5, compartment 3, or on the forklift on the way to him. Thanks to the supporting MES system, waste due to transportation is prevented, and the production processes improved with regard to LEAN production.
In addition, all times allocated to transport processes in production is recorded and is available for analysis. These times are therefore not only directly available to logistics, but also, for example, to production planners so that transport between the individual steps of a production order can be better planned. Within an Industry 4.0 context, advanced MES software like that from PROXIA Software AG today links all production processes and creates the basis for a continuous improvement process and a Smart Factory.
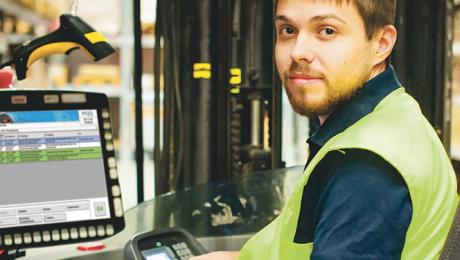
PROXIA Internal transport logistics
Storage and transport processes in companies can be very straightforward, but sometimes not! The heart of the lean philosophy is the prevention of waste in all company processes. As order numbers rise, the production process overview is quickly lost. With regard to storage and transport, questions arise such as where are the semi-finished goods kept, because we need complete the current step?
A high-tech MES system within an all-round LEAN concept can help answer this question.
The current production standard on the test bench
A specific example shows what is meant by “standard” in many companies today: An employee, let’s call him Mr Müller, walks through production with a clipboard. His task is to determine where semi-finished goods are located in production, to which production order they belong, and which machine should be used to process this order next. Production orders consist of a range of processing steps. If there is a large machine pool and a normally high number of production orders for the machines and plant, a lot of semi-finished goods are stockpiled, and it is extremely difficult to manage these efficiently and transparently using this method.
Therefore, no one in production, not even Mr Müller, has a complete overview of the storage and transport of semi-finished goods. As there are no defined storage areas, operators put the semi-finished goods wherever they can find space. Mostly they remain on the machine on which they have just been processed until they are required by the next step. If this is not immediately the case, or a very large volume has been produced, this machine can sometimes be put out of use due to lack of space. The responsible operators may also decide to make space to house the parts. In the worst case scenario, the operator leaves his work area to look for Mr Müller or a forklift driver who can help him transport the parts. As there are no defined storage areas, the operator puts the goods wherever there is space. He might then forget to record the storage location because, e.g. he takes a break. As a result, the machine is not only out of action, but Mr Müller is left with the task of finding the parts.
The main thrust of a lean philosophy, the prevention of waste in all company processes, is not applied in this example. Lean production applies this philosophy to production processes. The example described above includes many types of waste relating to the lean production concept, the most obvious being:
- Movement – Mr Müller spends the whole day in production, trying to find semi-finished goods
- Stock – Storage of semi-finished goods between processes in undefined locations
- Transport – Semi-finished goods appear to be kept and transported between processes without a defined plan
Production standard is now Industry 4.0 capable with MES
In order to reduce these types of waste to an absolute minimum, high-tech MES solutions not only support the planning and processing of production orders, but also support internal transport logistics within the lean philosophy concept. For example, production logistics, e.g. forklifts, can be directly linked to the MES system using an extended operator terminal. This enables the operator to request transport from the forklift driver direct from the BDE terminal without having to leave his work area. The relevant employee can also see exactly where the semi-finished goods he requires for the following process are located, therefore allowing “chaotic warehousing” in production. Only the temporary storage location of the specific semi-finished product needs to be recorded in the MES system. Everyone involved in the process can then see where the relevant material is located at any time.
Mr Müller in our example can now turn his attention to other tasks because searching for material is a thing of the past. The operator’s terminal shows the location of the required semi-finished goods or materials, whether they are on the machine used for the previous process, at storage location C22, shelf 5, compartment 3, or on the forklift on the way to him. Thanks to the supporting MES system, waste due to transportation is prevented, and the production processes improved with regard to LEAN production.
In addition, all times allocated to transport processes in production is recorded and is available for analysis. These times are therefore not only directly available to logistics, but also, for example, to production planners so that transport between the individual steps of a production order can be better planned. Within an Industry 4.0 context, advanced MES software like that from PROXIA Software AG today links all production processes and creates the basis for a continuous improvement process and a Smart Factory.