EMO 2019: Stäubli to showcase robots for machine loading and joined-up production
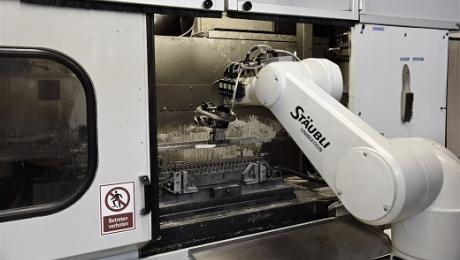
Intelligent robotic solutions in and around the machine
EMO is the world’s leading trade fair for the metalworking industry; Stäubli will be showcasing two main areas of interest: new robots for classic machine loading duties, including the world premiere of the new HE version of the TS2-SCARA, and mobile robotic solutions for joined-up production.
The unique construction of the TX2 six-axis series makes it ideally suited to the special requirements that apply in metalworking, where direct contact with grinding dust, swarf and cooling lubricants is unavoidable. With the six-axis TX2s, applications can be implemented reliably inside a machining center where any other standard robot wouldn´t be able to cope with the punishing conditions.
The advantage of the TX2 six-axis machines is their enclosed design, the internal wiring, the connections under the robot pedestal and their high protection category. This is now also applicable to the brand new four-axis robots of the TS2 series. As a result, Stäubli can now offer SCARAs for even the most demanding tasks in machine automation.
This development has been made possible by the total redesign of the four-axis series. They are now equipped with Stäubli’s proprietary JCS drive technology, developed and built in-house, which was previously reserved for the six-axis models. This technology is the key to the enormous performance gain of the TS2 SCARAs. Hollow shaft technology has facilitated an enclosed structure, which has made external cabling a thing of the past.
Four-axis robots now available as HE versions
This pioneering design paves the way for an interesting option that has so far not featured on the SCARA list. For applications in which the robots are permanently exposed to cooling lubricants, Stäubli recommends the HE (Humid Environment) versions with their additional level of protection. To ensure maintenance free operation of the new four-axis robots, even where they are integrated into machining centers, they incorporate stainless steel parts, toughened seals and specially coated housing panels. With the arrival of the HE version of its four-axis TS2 machine, Stäubli has filled a gap in the market and is now able to supply all robot kinematics in this special protected design.
In order to provide an optimal solution for all machine sizes, the new robot series comprises of four models, the TS2-40, TS2-60, TS2-80 and TS2-100. The previous series covered ranges of 400 to 800 millimeters, but this has now been extended to a working radius of 1,000 millimeters with the added addition of the TS2-100. Overall, the new SCARAs are considerably more compact than their predecessors and are therefore optimally equipped for the automation of machine tools and machining centers.
Connecting up machinery with the use of mobile robot systems
Now ready for series production and certain to be one of the main attractions at EMO, the HelMo mobile robot system proves that, with Stäubli, the future of machine automation can become a reality today.
HelMo can maneuver and navigate autonomously, monitoring its environment by using three integrated laser scanners. Equipped with a six-axis robot of the TX2 series, HelMo can carry out all types of work, including roles that call for direct human-robot collaboration.
Machine loading and linking is a prime example of how the mobile robot can replace obsolete production scenarios. Whereas forklifts, manual tool and workpiece handling, conveyor systems and fixed automation solutions were still used in the recent past, HelMo is now able to manage the entire task spectrum. It can network production, fetch tools from a magazine, bring them to the machine, manage the loading and unloading of machine tools and connect up the process as appropriate.
Multiple mobile robots can serve complete production lines by communicating with each other via an ERP system. HelMo will enable users to achieve smart production in future Industry 4.0 environments, with a significant gain in autonomy, flexibility and productivity. A complex safety package is included to meet the rigorous specifications that apply. All safety functions conform to the stringent SIL3/PLe category.
Open interfaces to all control systems
Stäubli’s ready-to-plug solutions uniVAL drive and uniVALplc meets the demands from many users for a uniform control platform for machine tools and robots. The result is that all Stäubli kinematics can be operated via the multi-axis controls of the machine tool or via programmable logic controllers from renowned suppliers such as Siemens and Beckhoff.
Integration of the robots into the relevant control system is easier than ever before. If robot control is to be performed via a multi-axis unit, uniVAL drive is the appropriate choice. UniVAL drive allows the machine tool controller to take over the robot controller and operates the individual robot axes via bus systems such as Sercos3, Ethercat, Powerlink and Profinet.
A further development from Stäubli is uniVAL plc. This solution with its predefined interface allows the operation of robots via programmable logic controllers. The programming of the robots is carried out in a user-friendly manner by use of function blocks while Stäubli´s path planning remains active in the background.
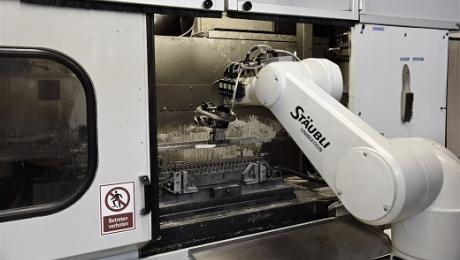
Intelligent robotic solutions in and around the machine
EMO is the world’s leading trade fair for the metalworking industry; Stäubli will be showcasing two main areas of interest: new robots for classic machine loading duties, including the world premiere of the new HE version of the TS2-SCARA, and mobile robotic solutions for joined-up production.
The unique construction of the TX2 six-axis series makes it ideally suited to the special requirements that apply in metalworking, where direct contact with grinding dust, swarf and cooling lubricants is unavoidable. With the six-axis TX2s, applications can be implemented reliably inside a machining center where any other standard robot wouldn´t be able to cope with the punishing conditions.
The advantage of the TX2 six-axis machines is their enclosed design, the internal wiring, the connections under the robot pedestal and their high protection category. This is now also applicable to the brand new four-axis robots of the TS2 series. As a result, Stäubli can now offer SCARAs for even the most demanding tasks in machine automation.
This development has been made possible by the total redesign of the four-axis series. They are now equipped with Stäubli’s proprietary JCS drive technology, developed and built in-house, which was previously reserved for the six-axis models. This technology is the key to the enormous performance gain of the TS2 SCARAs. Hollow shaft technology has facilitated an enclosed structure, which has made external cabling a thing of the past.
Four-axis robots now available as HE versions
This pioneering design paves the way for an interesting option that has so far not featured on the SCARA list. For applications in which the robots are permanently exposed to cooling lubricants, Stäubli recommends the HE (Humid Environment) versions with their additional level of protection. To ensure maintenance free operation of the new four-axis robots, even where they are integrated into machining centers, they incorporate stainless steel parts, toughened seals and specially coated housing panels. With the arrival of the HE version of its four-axis TS2 machine, Stäubli has filled a gap in the market and is now able to supply all robot kinematics in this special protected design.
In order to provide an optimal solution for all machine sizes, the new robot series comprises of four models, the TS2-40, TS2-60, TS2-80 and TS2-100. The previous series covered ranges of 400 to 800 millimeters, but this has now been extended to a working radius of 1,000 millimeters with the added addition of the TS2-100. Overall, the new SCARAs are considerably more compact than their predecessors and are therefore optimally equipped for the automation of machine tools and machining centers.
Connecting up machinery with the use of mobile robot systems
Now ready for series production and certain to be one of the main attractions at EMO, the HelMo mobile robot system proves that, with Stäubli, the future of machine automation can become a reality today.
HelMo can maneuver and navigate autonomously, monitoring its environment by using three integrated laser scanners. Equipped with a six-axis robot of the TX2 series, HelMo can carry out all types of work, including roles that call for direct human-robot collaboration.
Machine loading and linking is a prime example of how the mobile robot can replace obsolete production scenarios. Whereas forklifts, manual tool and workpiece handling, conveyor systems and fixed automation solutions were still used in the recent past, HelMo is now able to manage the entire task spectrum. It can network production, fetch tools from a magazine, bring them to the machine, manage the loading and unloading of machine tools and connect up the process as appropriate.
Multiple mobile robots can serve complete production lines by communicating with each other via an ERP system. HelMo will enable users to achieve smart production in future Industry 4.0 environments, with a significant gain in autonomy, flexibility and productivity. A complex safety package is included to meet the rigorous specifications that apply. All safety functions conform to the stringent SIL3/PLe category.
Open interfaces to all control systems
Stäubli’s ready-to-plug solutions uniVAL drive and uniVALplc meets the demands from many users for a uniform control platform for machine tools and robots. The result is that all Stäubli kinematics can be operated via the multi-axis controls of the machine tool or via programmable logic controllers from renowned suppliers such as Siemens and Beckhoff.
Integration of the robots into the relevant control system is easier than ever before. If robot control is to be performed via a multi-axis unit, uniVAL drive is the appropriate choice. UniVAL drive allows the machine tool controller to take over the robot controller and operates the individual robot axes via bus systems such as Sercos3, Ethercat, Powerlink and Profinet.
A further development from Stäubli is uniVAL plc. This solution with its predefined interface allows the operation of robots via programmable logic controllers. The programming of the robots is carried out in a user-friendly manner by use of function blocks while Stäubli´s path planning remains active in the background.