Liebherr gets hands-on
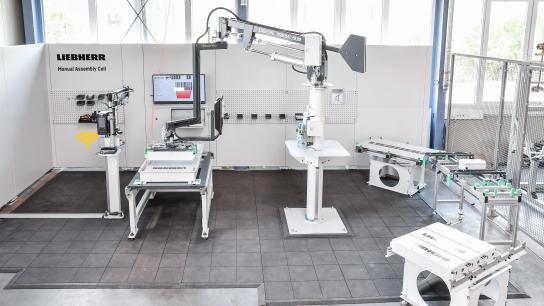
Manual assembly stations are also needed for highly automated assembly lines in the automotive industry, not every assembly step can be automated in a productive or cost-effective manner. As a specialist in the automation of battery pack assembly, Liebherr-Verzahntechnik GmbH has expanded its portfolio to offer users versatile solutions for smart, digitally supported manual assembly.
Many assembly processes within e-mobility cannot be automated or can only be automated with great difficulty. This is particularly pertinent to complex or non-rigid components, for assembly positions that are difficult to access, and for components with several variants. For these reasons, there is still a high proportion of manual assembly in battery pack assembly lines where it is essential for a cost-effective overall concept. Additionally, high-voltage battery systems are a relatively new product whose production volumes, variants, product designs, and manufacturing processes change rapidly as development continues. Manual assembly stations make greater flexibility and rapid adaptation to changing market requirements possible.
Product configurator for manual assembly of high voltage battery packs
“Coming in at around a third of the overall value of the vehicle, batteries are the most expensive single component in an e-vehicle. That’s why process reliability is a particularly high priority for customers,” states Viktor Bayrhof, Product Manager for Automation Systems at Liebherr-Verzahntechnik GmbH. Consequently, the challenges presented to manual assembly stations are very complex. “It’s not about just assembling a few parts by hand. Nowadays you have to consider topics such as worker assistance systems, data acquisition and digitalization.”
Liebherr has studied in minute detail the requirements in terms of (HV) safety, ergonomics, and methods for analyzing manual work steps. Using this as a basis, the company will launch a product configurator specifically designed for the integration of manual assembly stations in battery pack assembly lines.
Staying flexible with the help of matrices
Liebherr has been supplying automated systems for powertrains to the automotive industry for the series production of components for decades. Now, the transformation to battery-powered electric drives is bringing major changes which also impact the company’s product and service portfolio. “In the past few years, we have built up our skill set in automated process handling of new technologies. Now we are expanding our portfolio with a further building block: manual assembly”, explains Bayrhof. Liebherr’s modular system can be freely adapted to meet the customer’s requirements. With screen-based worker guidance, systems for determining the position of tools and hands, light-guided assistance for picking or placing components (“pick-to-light”/”put-to-light”) as well as evaluation and logging of work steps and tool parameters.
When planning the layout of the overall assembly plant, potential expansion stages are also considered so further stations can be added as the number of production units increases. The trend is toward “matrix assembly,” meaning that assembly stations are networked and can be interlinked freely; new component variants, new technologies and additional stations can be integrated more easily. “We configure the entire system from top to bottom and can react to the individual requirements of the customer using automated or manual assembly stations”, says Bayrhof.
... read more here!
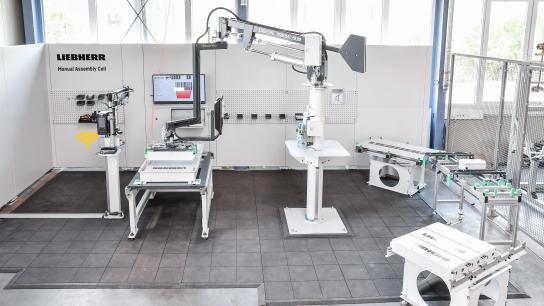
Manual assembly stations are also needed for highly automated assembly lines in the automotive industry, not every assembly step can be automated in a productive or cost-effective manner. As a specialist in the automation of battery pack assembly, Liebherr-Verzahntechnik GmbH has expanded its portfolio to offer users versatile solutions for smart, digitally supported manual assembly.
Many assembly processes within e-mobility cannot be automated or can only be automated with great difficulty. This is particularly pertinent to complex or non-rigid components, for assembly positions that are difficult to access, and for components with several variants. For these reasons, there is still a high proportion of manual assembly in battery pack assembly lines where it is essential for a cost-effective overall concept. Additionally, high-voltage battery systems are a relatively new product whose production volumes, variants, product designs, and manufacturing processes change rapidly as development continues. Manual assembly stations make greater flexibility and rapid adaptation to changing market requirements possible.
Product configurator for manual assembly of high voltage battery packs
“Coming in at around a third of the overall value of the vehicle, batteries are the most expensive single component in an e-vehicle. That’s why process reliability is a particularly high priority for customers,” states Viktor Bayrhof, Product Manager for Automation Systems at Liebherr-Verzahntechnik GmbH. Consequently, the challenges presented to manual assembly stations are very complex. “It’s not about just assembling a few parts by hand. Nowadays you have to consider topics such as worker assistance systems, data acquisition and digitalization.”
Liebherr has studied in minute detail the requirements in terms of (HV) safety, ergonomics, and methods for analyzing manual work steps. Using this as a basis, the company will launch a product configurator specifically designed for the integration of manual assembly stations in battery pack assembly lines.
Staying flexible with the help of matrices
Liebherr has been supplying automated systems for powertrains to the automotive industry for the series production of components for decades. Now, the transformation to battery-powered electric drives is bringing major changes which also impact the company’s product and service portfolio. “In the past few years, we have built up our skill set in automated process handling of new technologies. Now we are expanding our portfolio with a further building block: manual assembly”, explains Bayrhof. Liebherr’s modular system can be freely adapted to meet the customer’s requirements. With screen-based worker guidance, systems for determining the position of tools and hands, light-guided assistance for picking or placing components (“pick-to-light”/”put-to-light”) as well as evaluation and logging of work steps and tool parameters.
When planning the layout of the overall assembly plant, potential expansion stages are also considered so further stations can be added as the number of production units increases. The trend is toward “matrix assembly,” meaning that assembly stations are networked and can be interlinked freely; new component variants, new technologies and additional stations can be integrated more easily. “We configure the entire system from top to bottom and can react to the individual requirements of the customer using automated or manual assembly stations”, says Bayrhof.
... read more here!