Been a while since I posted progress or pictures, but I have been busy giving students final exams and correcting them.
I was working on my machine, but just diodn't ahve time to post, so here is where everything stands so far:
Started out the week with two mistakes:
First when I drilled the Drive assembly (Part E) for the Gantry bottom my bolt location was off, not a lot but enough so that the bolts would not go through the holes.MY apologies for the poor picture quality.

Next day made a new one of those.
Then I followed taht up by having the motor mount holes out of alignment for the gantry sides. Every other hole was spot on.

Made new ones of those and they lined up perfectly.
Today I was able to get the entire gantry assembled and sliding.
Table top and Y axis with the gantry side.

Gantry side and X axis rail.
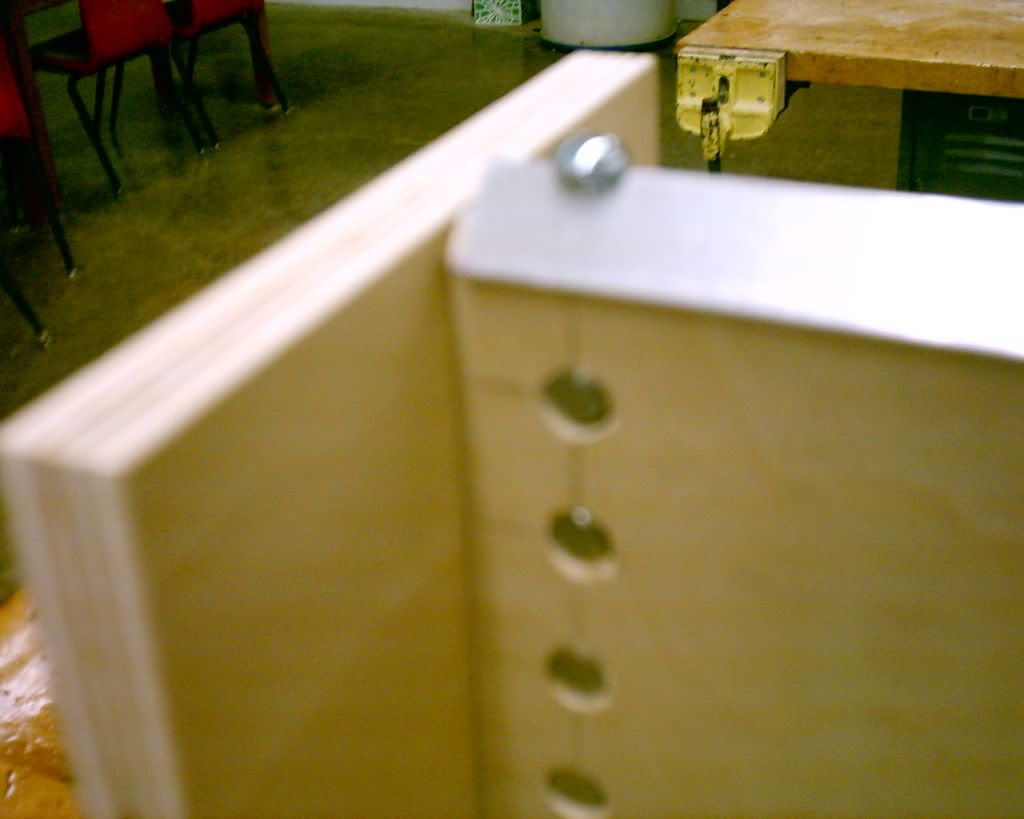
Front view of Machine.

Back view

I have discoved that I am missing some 3" bolts and about 25 or so 1/4" nuts, but it seems I do hafve extra cross dowels and 2"bolts.
Does anyone think that using the 2" instead of the 3" will impair the machines strength and or accuracy?