I was able to accomplish the basics of what I needed by center drilling, then changing to the chucked twist drill and using the short thrust stroke of the tailstock screw, then just loosening the tailstock-to-rail screw and hand-ramming it into the Delrin, pulling out to clear, and repeating.
The trouble I have now is parting. I have the 3.25" dia 4-jaw indy chuck (but it's not the official "Sherline lathe" 3.1"):
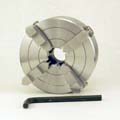
The problem here is that the only orientation which doesn't strike the bed is the jaws with the steps on the inside. This does not provide enough grip to stabilize the Delrin without a tailstock, not in this length. Tightening further only makes the Delrin pop out.
The problem in the parting is that you can't use a tailstock. Well, I tried anyways with the tailstock pressure minimal. Eh, the results didn't put me in fear of my life or anything. But even though the parting tool went in at 90 deg to the work, the tip walked WAY off to the right, leaving the left side concave and the right side convex when all was done. This happened irrespective of how fast it was driven in.
Why did the parting tool's tip walk so much? I see Sherline recommended a 5 deg angle on the blade when viewed from the top. I'm not sure I see why, that would seem to make it cut unevenly to me. I can't tell for sure what angle my blade does or does not have.
I kinda wanna just hold a hacksaw over it now and drop it down to cut it...
I found that with.... I guess it's about 3" long part with a 3/4" new diameter- the end face couldn't be finished either because again the jaws can't hold that stable without a tailstock, but the SteadyRest will probably cure that. In fact I might be able to use the SteadyRest instead of the tailstock for the parting operating, right? Still won't fix the real problem of the parting tool wandering though.